De plus en plus de membres du forum possèdent un flat4, nous motivant à réaliser un article sur le montage d’un moteur « perfo ». Bien entendu il existe sur le marché et sur Internet une grande quantité d’articles mais souvent ceux-ci sont peu accessibles ou ne présentent pas les explications nécessaires au montage d’un tel moteur. Nous allons essayer de parler de prix et de donner des références utilisables par tous. Toutefois afin de réduire les coûts du montage, certaines opérations seront réalisées grâces à des bons plans. Mais dans le monde vw pratiquement tout le monde a des bons plans non ?
Bref, nous profitons de la restauration d’une berline de 1960 pour monter un nouveau moteur car comme vous vous en doutez le petit 1200cc original ne sera pas à l’ordre du jour. Afin de concrétiser ce projet j’ai fait appel à Nicolas, amateur averti de mécanique vw « kivabien ». Ensemble, nous traçons autour d’un café les grandes lignes du projet. A savoir, un moteur qui ne sera pas ridicule sur route mais pas destiné à faire des courses sur 400m. La boite à vitesse et le système d’embrayage devra rester dans la première phase plus ou moins d’origine.
La première idée très répandue allait vers un classique 1641cc, néanmoins efficace. Configuration simple car elle ne nécessite pas l’usinage du bloc moteur mais simplement le remplacement des pistons et des cylindres. De plus, l’épaisseur des chemises lui procure une excellente solidité, proche de celle d’origine. Mais comme le dit un célèbre préparateur du monde du 4 à plat un 1776 et c’est tout ! Nicolas me confie qu’il dispose de l’outil nécessaire afin d’usiner le bloc moteur et que cette opération peut être réalisée sans problème à domicile. Vu la différence de prix ridicule entre le kit Mahle 1641cc et 1776cc la décision est prise de prendre la plus grande cylindrée pour le projet. Le kit doit être forgé, car le rapport volumétrique sera changé. Après quelques recherches de fournisseurs, il s’est avéré que le kit cylindré pour un 1776cc coûte moins cher que le 1641cc et cela pour des éléments de même marque et de même qualité de réalisation.
Un autre point important est le choix de la carburation. Jouissant d’une expérience quotidienne avec la conduite de sa 1303 S, Nicolas préconise l’utilisation d’un kit Kadron (Empi) 40 pour le 1641cc. Il consiste d’un double système de carburation simple corps de marque solex monté sur des pipes Empi. Ce kit est populaire car il offre un excellent couple à bas régime (2000-2500RPM), est fiable au niveau des réglages et consomme relativement peu de carburant. Après réflexion et vu que la future cox n’est pas destinée à un usage quotidien, je pense me tourner plutôt vers un kit Weber 40 IDF double corps qui offrira un gain de puissance non négligeable. A contrario cette option va faire grimper la note finale de même que, bien entendu, la consommation du moteur et rendra un peu plus compliqués les réglages.
A l’intérieur du moteur nous trouverons des pièces qui ont fait leurs preuves et qui sont pratiquement indissociables à la réalisation d’un moteur perfo low budget, comme par exemple l’AAC Engle 110.
Au niveau des culasses le choix s’est porté suite à un article du dernier magazine VW Tech sur des 041, auxquelles on effectuera un petit fraisage 3 angles supplémentaire, afin d’améliorer la qualité du flux à l’admission. Pour le moment, pas question d’installer un carter d’huile supplémentaire mais l’utilisation d’une pompe huile à gros débit couplée à une cartouche filtrante montée sur le couvercle semble se révéler le meilleur rapport fiabilité/prix. De plus, cela nous permet de tester ce montage, boudé par les grands acteurs du mouvement aircooled actuel. Par sécurité ce montage devra impérativement être couplé à une sonde de pression d’huile afin d’avoir en permanence le contrôle du circuit. Car si la cartouche filtrante venait à sauter, le moteur ne serait plus lubrifié et donc la casse inévitable.
Pour l’échappement nous avons opté pour un 4/1 avec un silencieux Merged en grande partie pour le look, mais le diamètre des tubes est encore à définir afin d’avoir le meilleur rapport de compression possible. Ici, la règle populaire « plus c’est gros, plus c’est beau » n’est à nouveau pas applicable. Mais tout ceci a pour but de nous mettre l’eau à la bouche car nous sommes encore loin de l’assemblage dudit moteur.
Pour commencer, il nous faut une base moteur, l’utilisation du 1200cc d’origine ne peut pas être envisagée car c’est un simple admission en course 64mm et de toute façon il sera mis de côté afin de conserver les pièces originales de la voiture. Par chance, j’ai pu récupérer un bloc 1300cc AB qui semble après un rapide contrôle visuel et quelques manipulations (rotation et vérification approximative du jeu axial) très correct. Il est temps d’ouvrir une petite parenthèse : afin de répartir le budget et de faciliter la rédaction des articles, ce reportage sera divisé en plusieurs parties. En plus cela prendra le temps qu’il faudra, car le projet ne doit pas être bâclé !
Le bloc est rapatrié dans la ferme parentale de Nicolas face à un magnifique Flat 6 3200cc en cours de révision… Bref notre « petit » Flat 4 est d’abords vidangé de ses 2.5 litres d’huile qui accuse les années de stockage. Le bloc est nu ce qui signifie qu’il est totalement dépouillé des éléments satellites. Nous commençons par enlever les caches culbuteurs, ce qui nous laisse entrevoir les rampes de culbuteurs. En tournant la poulie nous plaçons les soupapes plus ou moins au même niveau afin d’éviter que la rampe soit sous contrainte lors du démontage. Ensuite commence le démontage du gros LEGO en dévissant les 2 écrous qui maintiennent la rampe. Une fois celles-ci retirées nous tirons en arrière les tiges de culbuteurs et préparons deux cartons (gauche, droite) afin de ne pas mélanger les pièces .
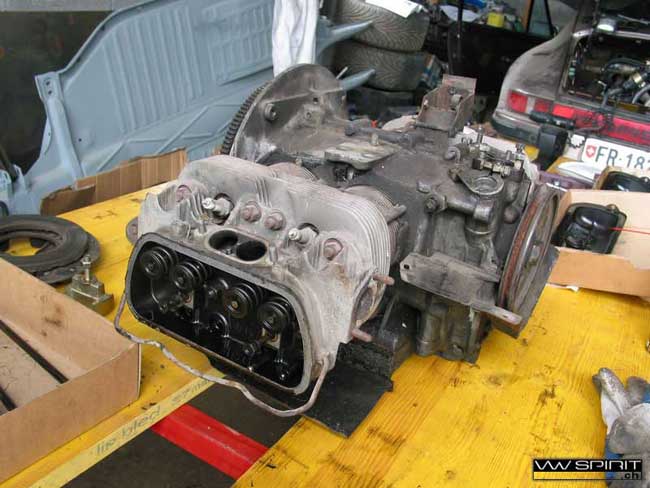

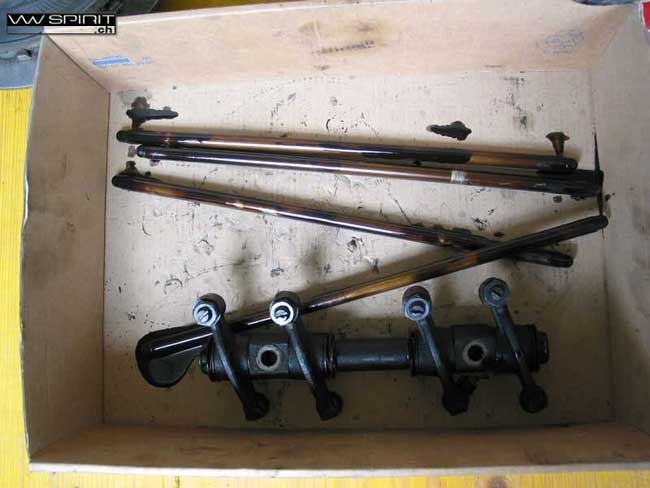
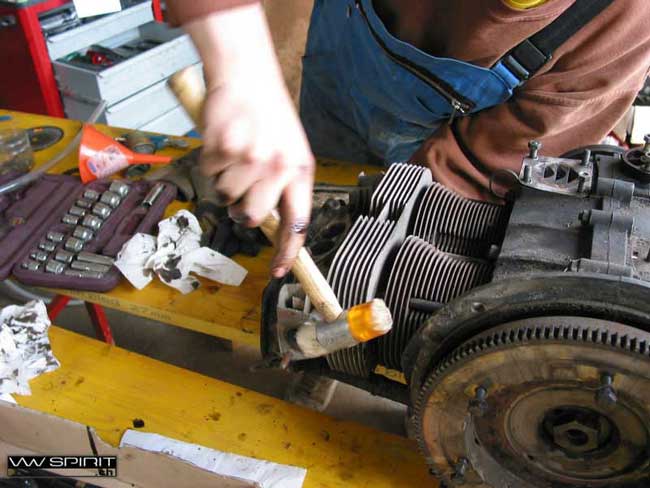
Avant d’aller plus loin, nous démontons l’embrayage afin d’avoir accès au boulon qui fait la liaison entre le volant moteur et le vilebrequin. Il est toujours plus facile de le desserrer alors que le moteur est complet, donc lourd et sur lequel on trouve facilement une prise. L’utilisation d’une déboulonneuse facilite grandement le travail, mais si le boulon est vraiment récalcitrants, il peut être décisif de l’asperger avec du dégrippant alors que vous êtes en train d’utiliser la déboulonneuse.
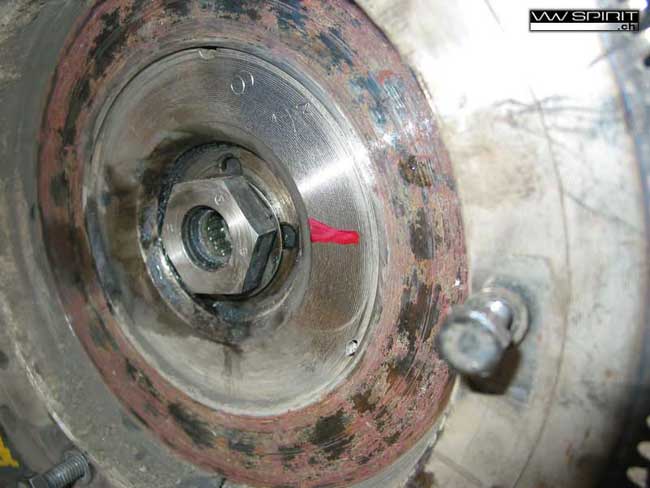
Nous passons ensuite aux culasses avec leurs huit écrous respectifs. Attention à ne pas faire levier avec un tournevis sur les ailettes pour les décoller. Prenez plutôt un maillet (alias gentle rubber mallet) et tapotez sur les parties solides, comme les goujons d’échappement, afin de les sortir bien dans l’axe. Nous avons maintenant les cylindres avec la tête des pistons apparents et la culasse dégagée. Une fois celle-ci complètement retirée nous pouvons regarder si elle est fendue, c’est toujours un grand moment de voir l’intérieur du moteur. Un peu comme lire les lignes d’un tronc d’un arbre scié. Nous prenons un peu d’essence pour nettoyer et dégraisser la tête du piston et les cylindres. Sur ceux-ci nous noterons les numéros de cylindres afin de ne pas les mélanger. Dans notre montage c’est peu important car des nouvelles pièces vont être montée. Mais Nicolas désirant préparer un 1200cc vitaminés en utilisant les pistons du 1300cc, nous notons quand même les choses dans les règles de l’art.
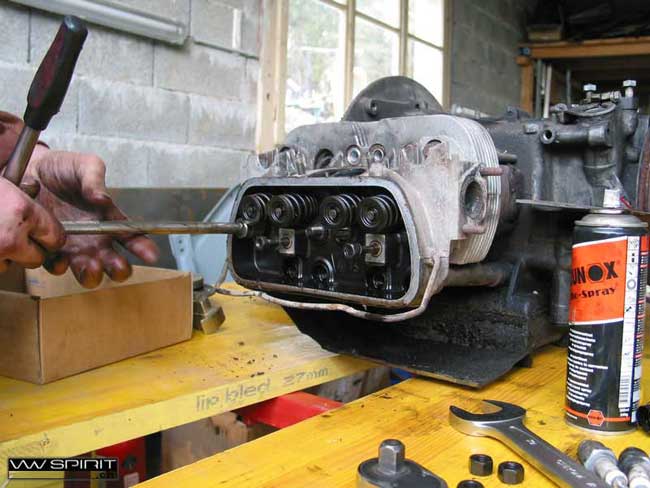
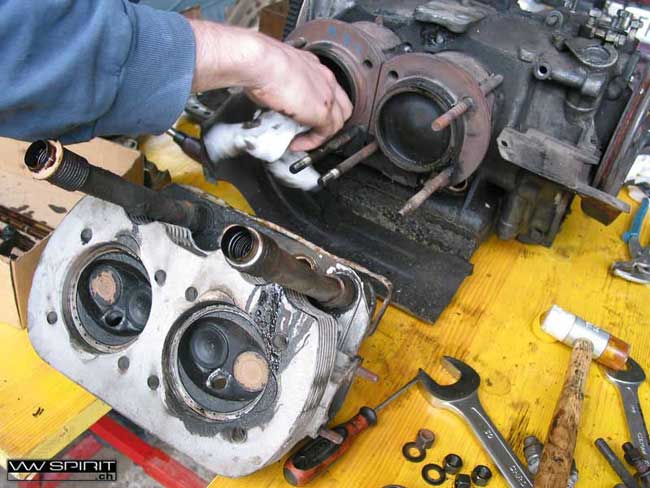
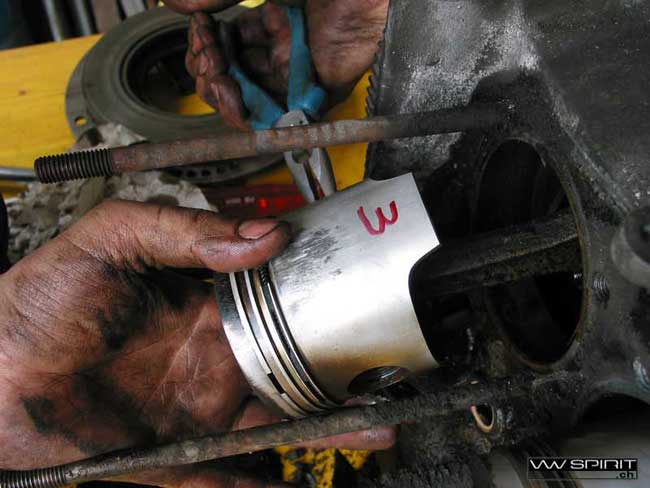
Pour sortir les cylindres nous pratiquons un léger mouvement de haut en bas et de gauche à droite afin de ne pas utiliser de marteau plastique. Toutefois si celui-ci ne vient pas, vous pouvez mettre un dégrippant en spray entre le bloc et le cylindre et tapoter avec parcimonie sur la base du cylindre afin de le décoller doucement. Une fois les deux côtés déculassés et les cylindres sortis, les pistons sont libres au bout des bielles. Une fois encore, il est important de bien vérifier l’état des pistons. Les nôtres sont parfaits, pas de traces de grippage et la segmentation semble comme neuve.
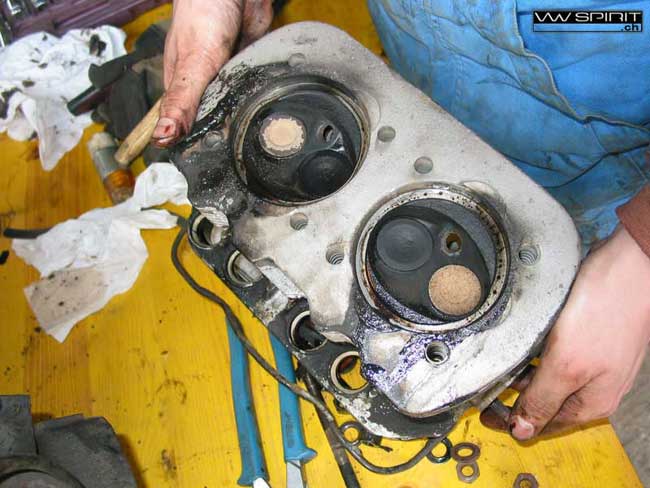
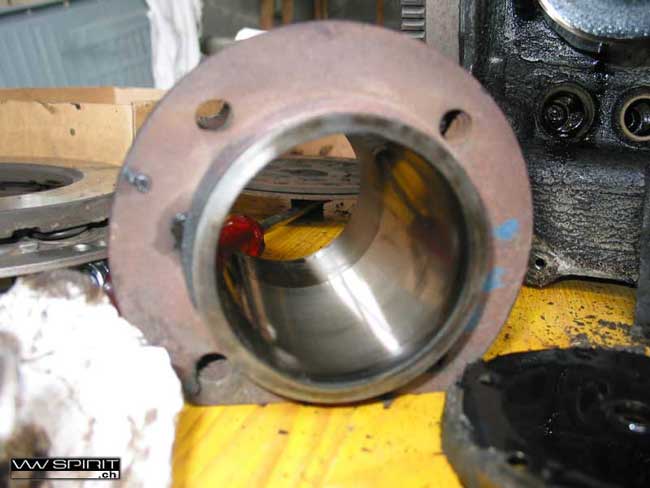
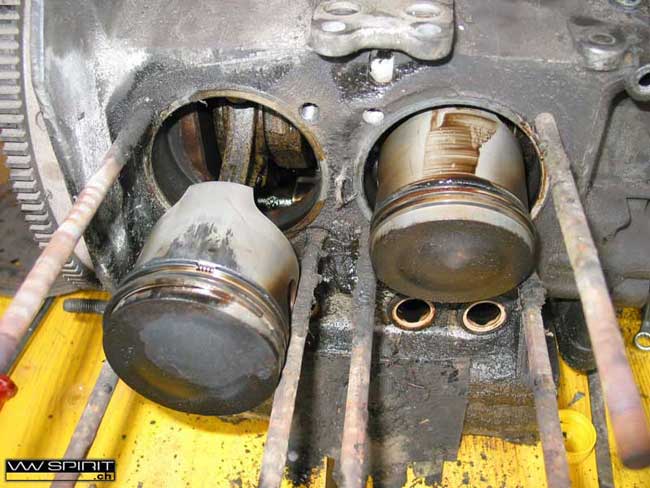
Nous pouvons retirer les pistons des bielles. Pour cette opération, nous utilisons une tige en acier d’un diamètre légèrement inférieur à 22 mm que nous venons appuyer sur l’axe du piston. Pratique, les goujons serviront d’appuis pour ne pas plier la bielle au moment où nous chasserons l’axe à l’aide de la tige et d’un marteau. Auparavant, il est important d’enlever les circlips qui assurent la fixation de l’axe dans le piston. Attention ces petits bouts de métal peuvent gicler et vous crever un œil, donc portez des lunettes pour cette opération, ou alors fermez les yeux.
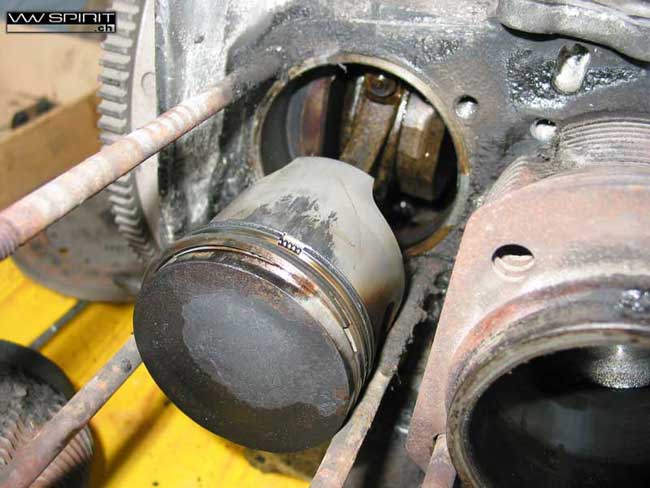
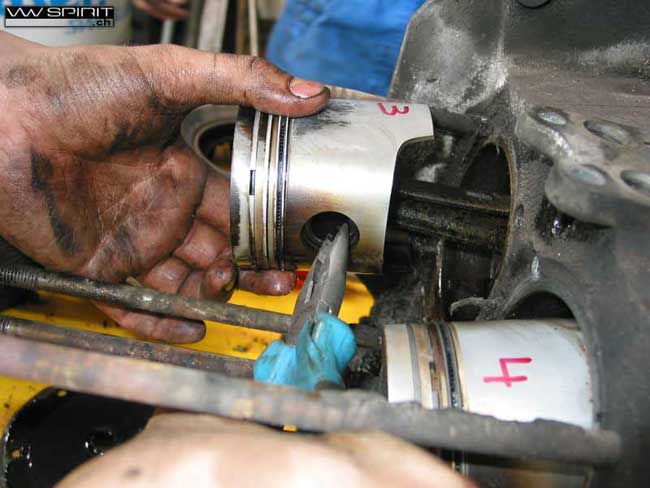
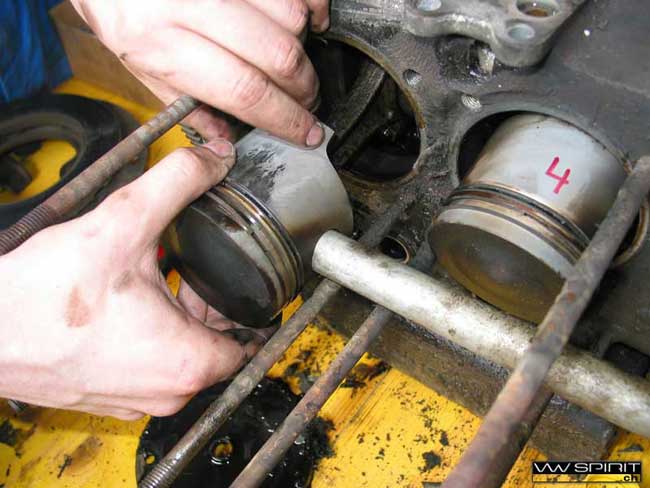
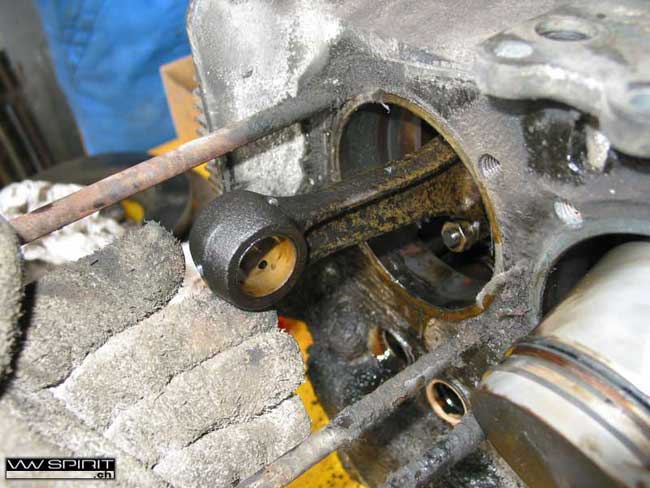
Maintenant vient le moment de retirer les goujons, le dégoujonnage™. Il n’existe malheureusement pas de dégoujonneuse™ et il ne reste qu’à utiliser le système écrou / contre écrou afin de les dévisser. C’est long, mais et il n’y en a que seize et nous l’accomplissons avec un sourire aux lèvres en pensant au mécano qui refait le moteur d’une 16.4 Veyron. Après un petit moment ils sont tous séparés du bloc et un seul filetage est venu avec… Pas trop grave car vu que nous devons usiner le bloc pour accueillir la nouvelle cylindrée il faudra de toute manière monter des inserts pour les goujons 8mm. Nous sortons ensuite la poulie en prenant soin de fixer le volant moteur à l’aide d’un outil spécifique. Il faut se résoudre à sortir la déboulonneuse pour la dévisser. Quelques coups de maillet de chaque coté et la voilà sortie…
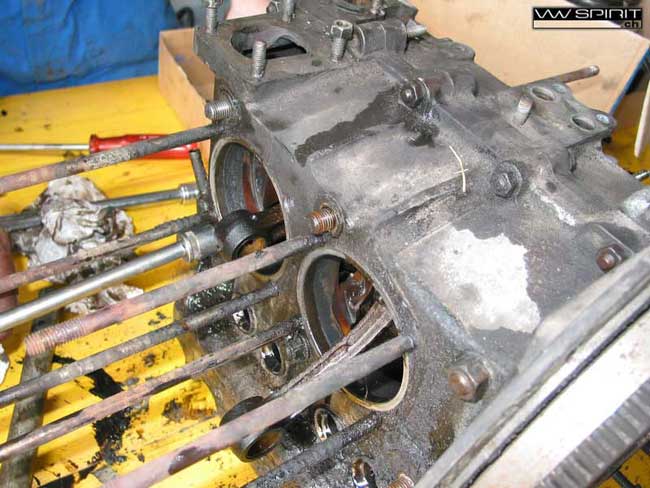
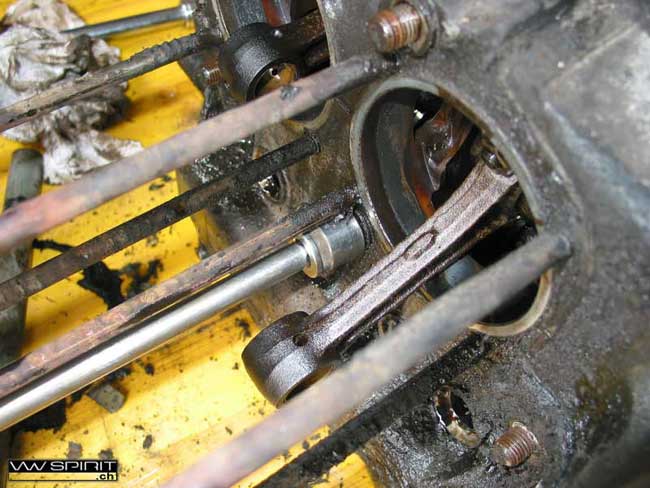
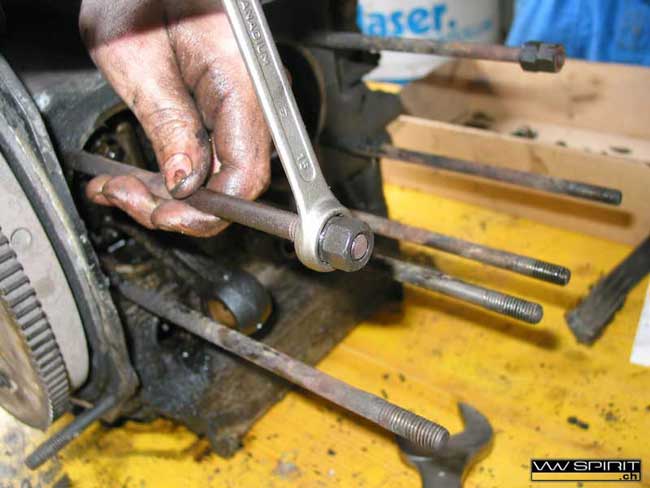
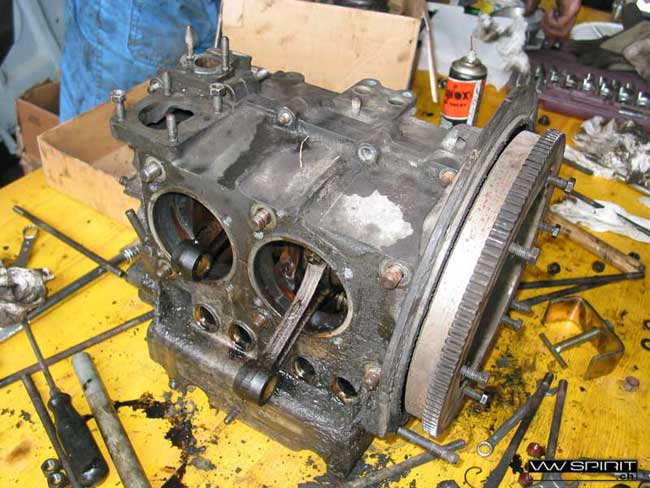
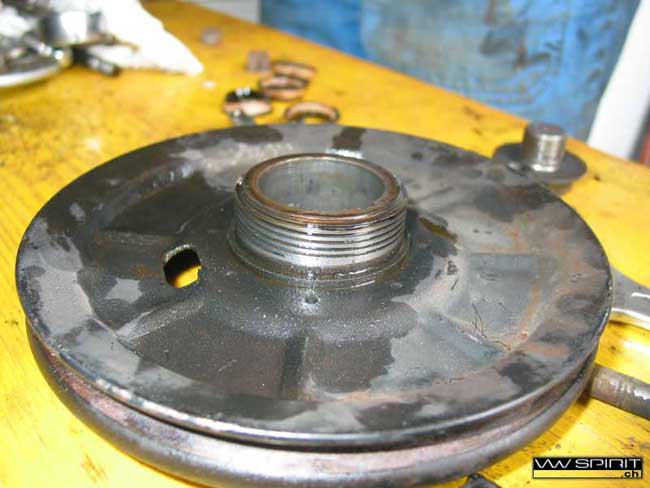
Nous attaquons ensuite le démontage de la pompe à huile en retirant le cache, puis les pignons et enfin à l’aide d’un extracteur la pompe elle-même. Quand ont a les outils cela aide beaucoup !
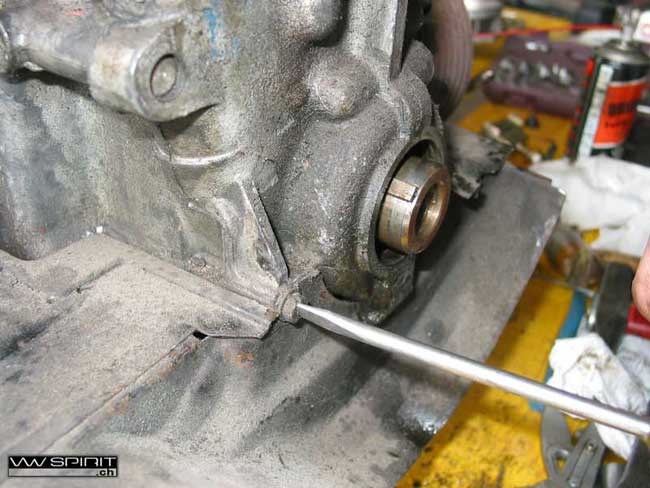
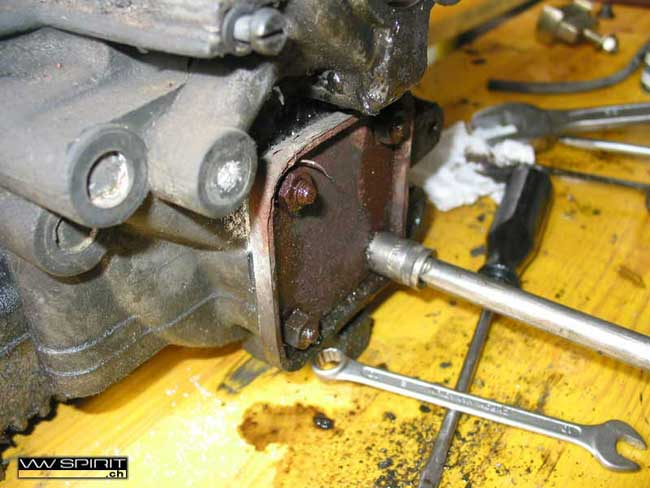
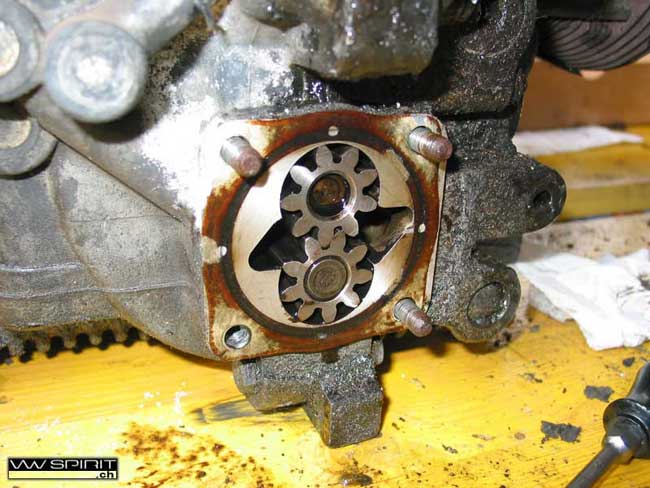
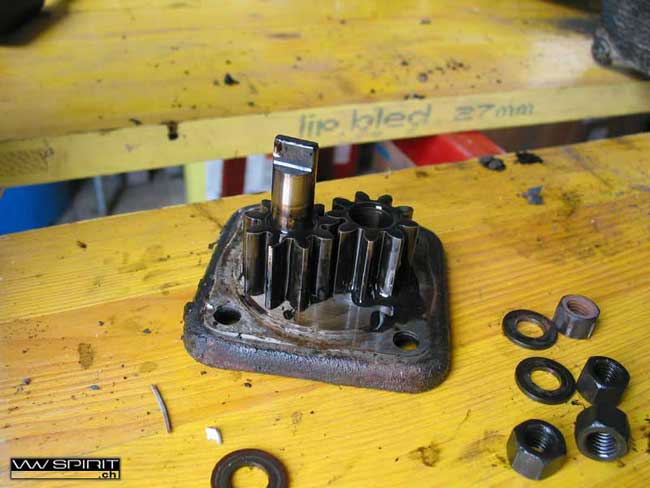
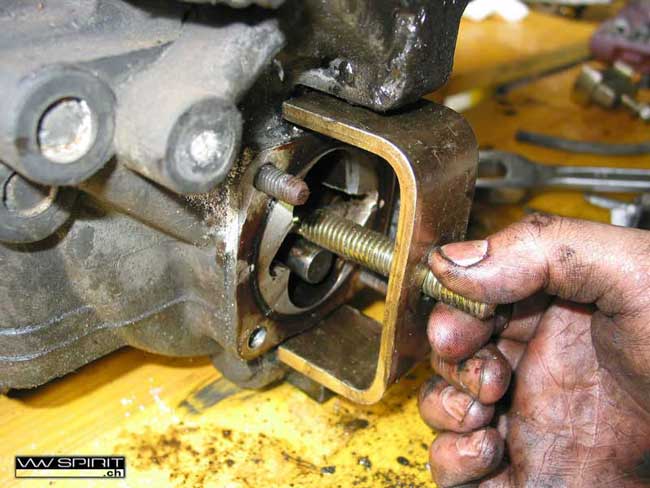
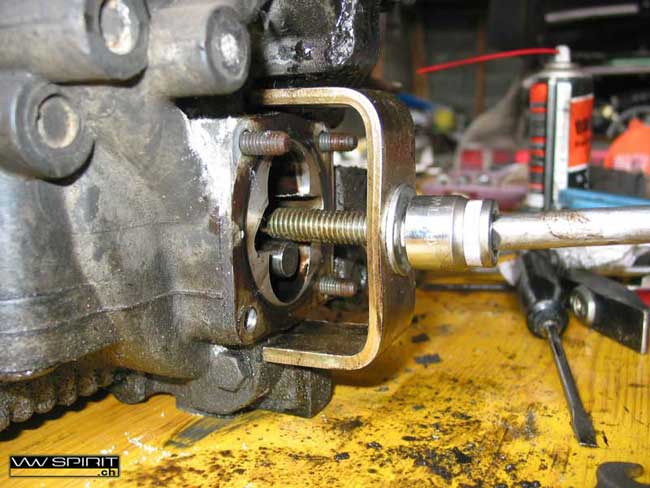
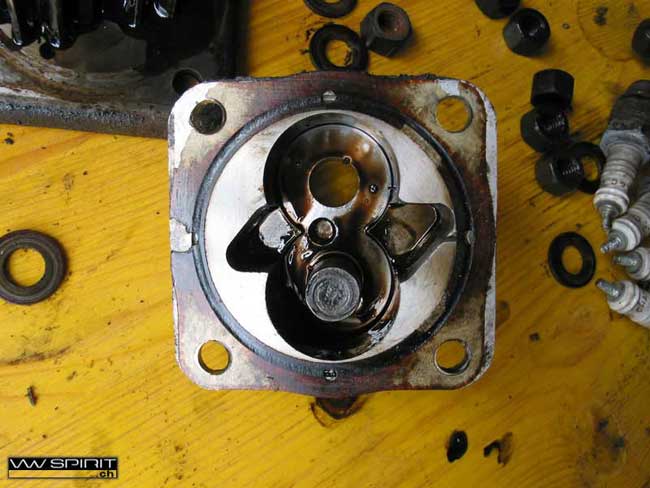
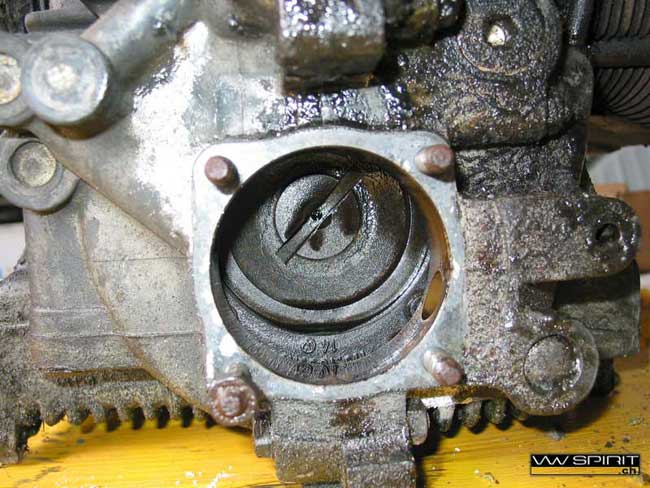
Voilà enfin le moment de séparer les carters en retirant les vis sur tout le pourtour. Vérifiez bien qu’elles soient toutes bien devisées car même en vérifiant deux fois il en reste toujours une. Nous prenons notre outil favoris à savoir le maillet et nous tapons sur des appuis solides afin d’ouvrir le bloc en deux. Je n’ai pas besoin de vous dire qu’il est strictement prohibé de faire levier sur le plan de joint sinon il faudra utiliser beaucoup de pâte à joint pour assurer l’étanchéité. Une fois le carter séparé, il faut tirer bien dans l’axe un des deux demi carters. Quatre poussoirs vont tomber lors de la séparation du carter, c’est normal. Pensez à récupérer la capsule qui se trouve au bout de la ligne d’aac, de même que l’axe d’allumeur, son ressort et ses deux rondelles. Nous avons préféré retirer les bielles avant la séparation afin d’éviter qu’elles ne tapent dans le moteur, plus particulièrement sur la surface plane de joint et dans les puits de cylindres, bien que dans notre cas, nous les usinerons à nouveau.
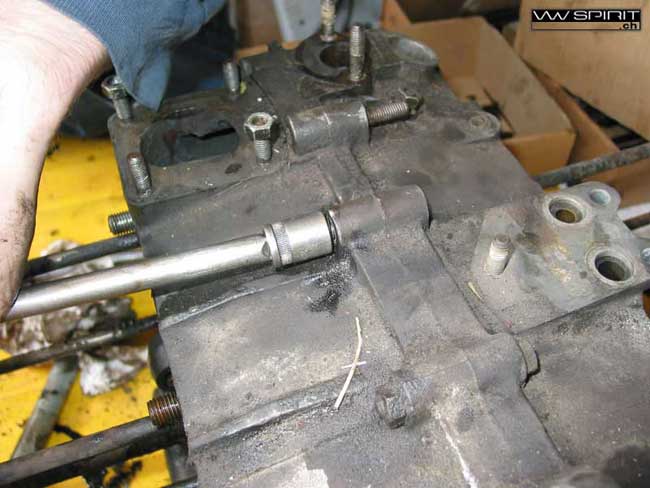

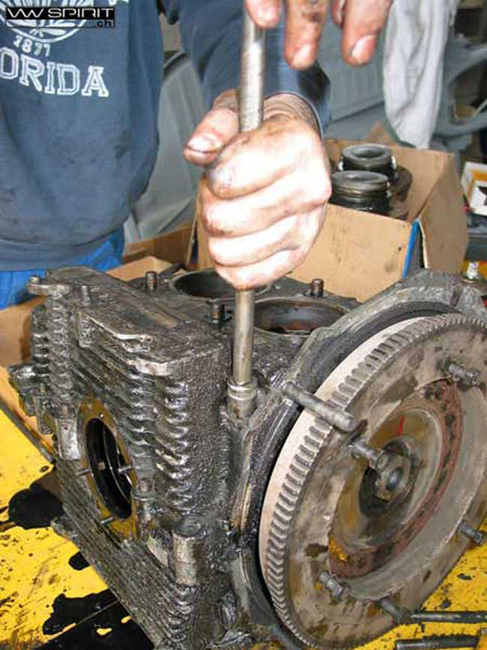
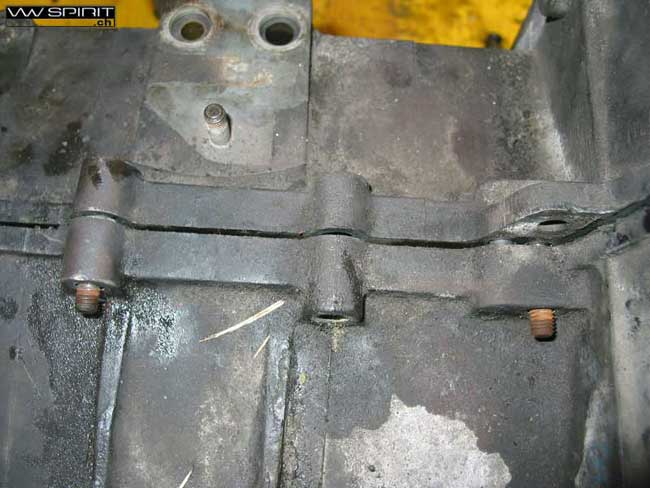
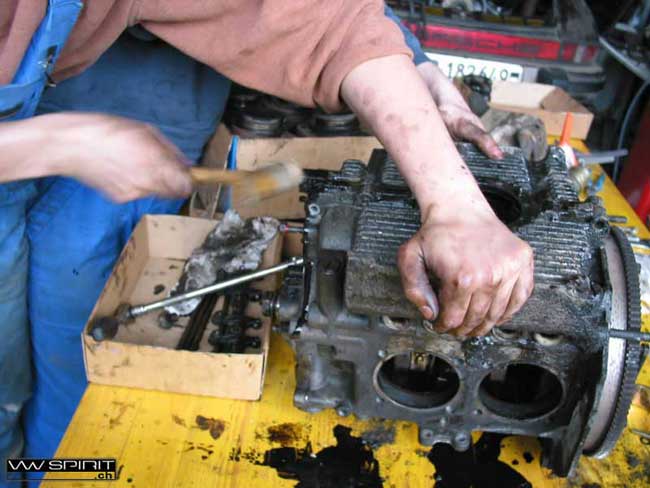
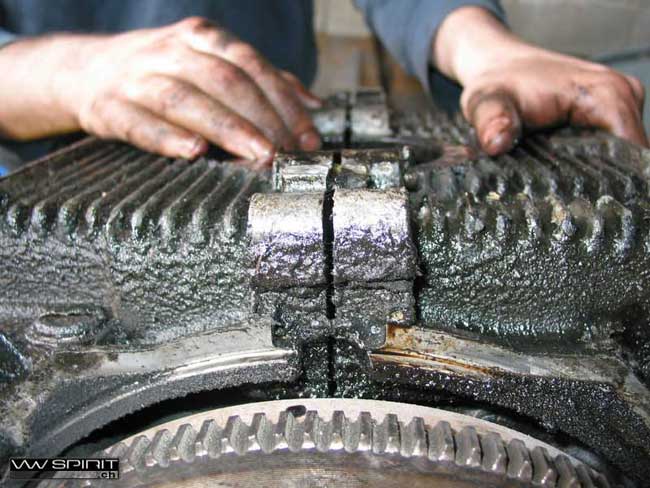
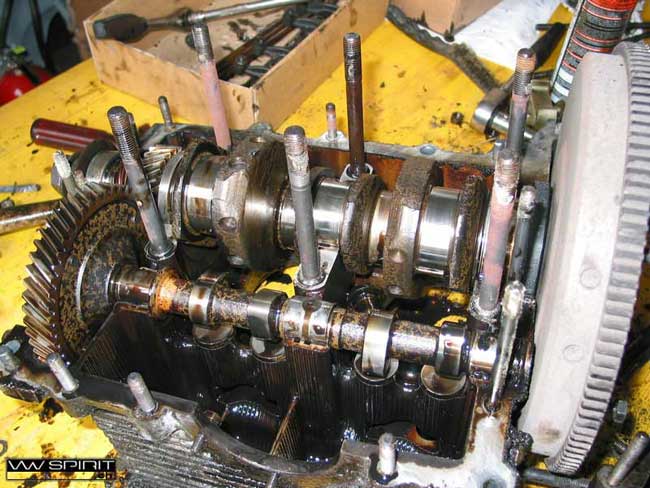
Ici aussi nous nettoyons à l’essence et notons soigneusement à quels cylindres les bielles appartiennent. A deux, nous sortons le volant moteur avec le vilo. C’est une belle sculpture et c’est plutôt lourd ! Un volant moteur allégé ne sert pas uniquement à avoir des montées en régime plus rapide…
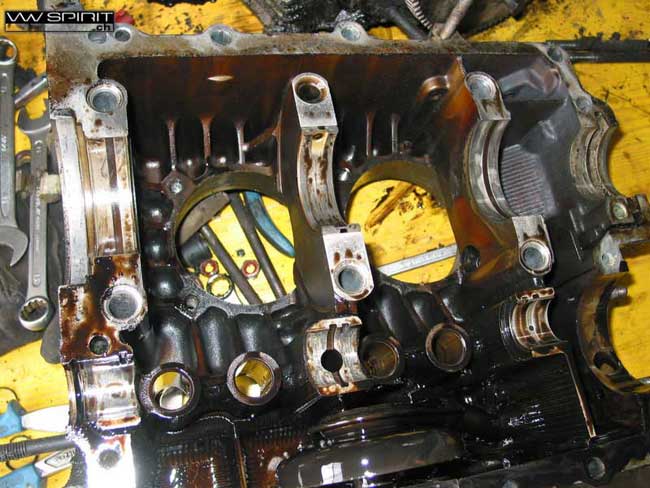
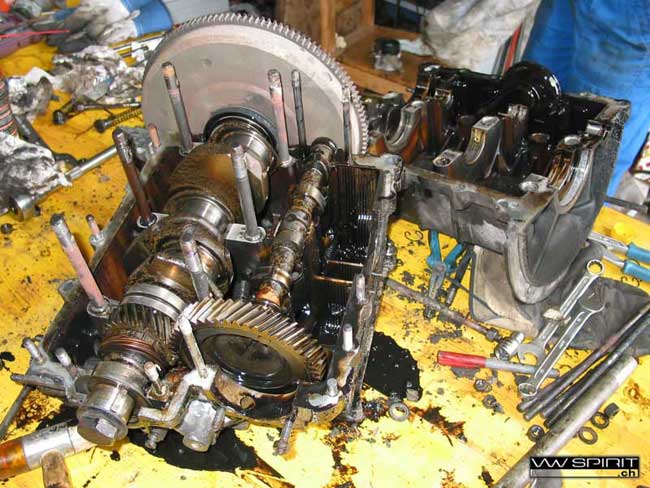
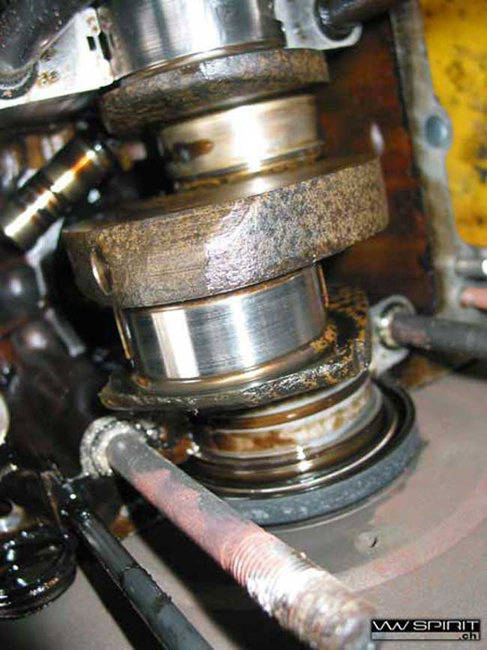
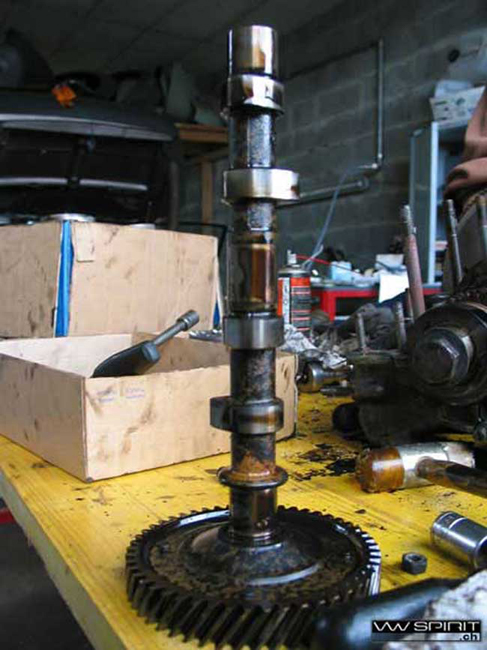
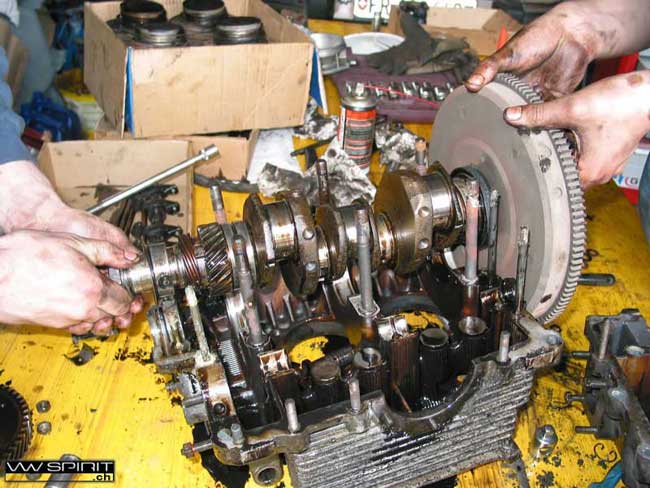
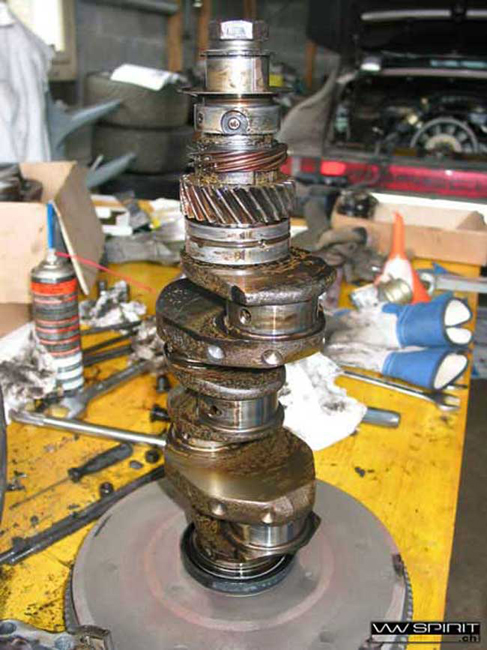
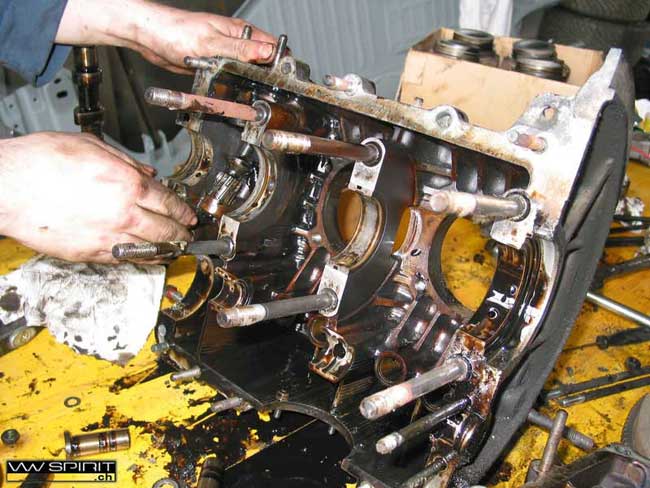
Et voilà, c’est la fin de la première partie! La prochaine fois, nous verrons la fin du démontage, le nettoyage et surtout toutes les mesures à faire afin de contrôler le bloc. |